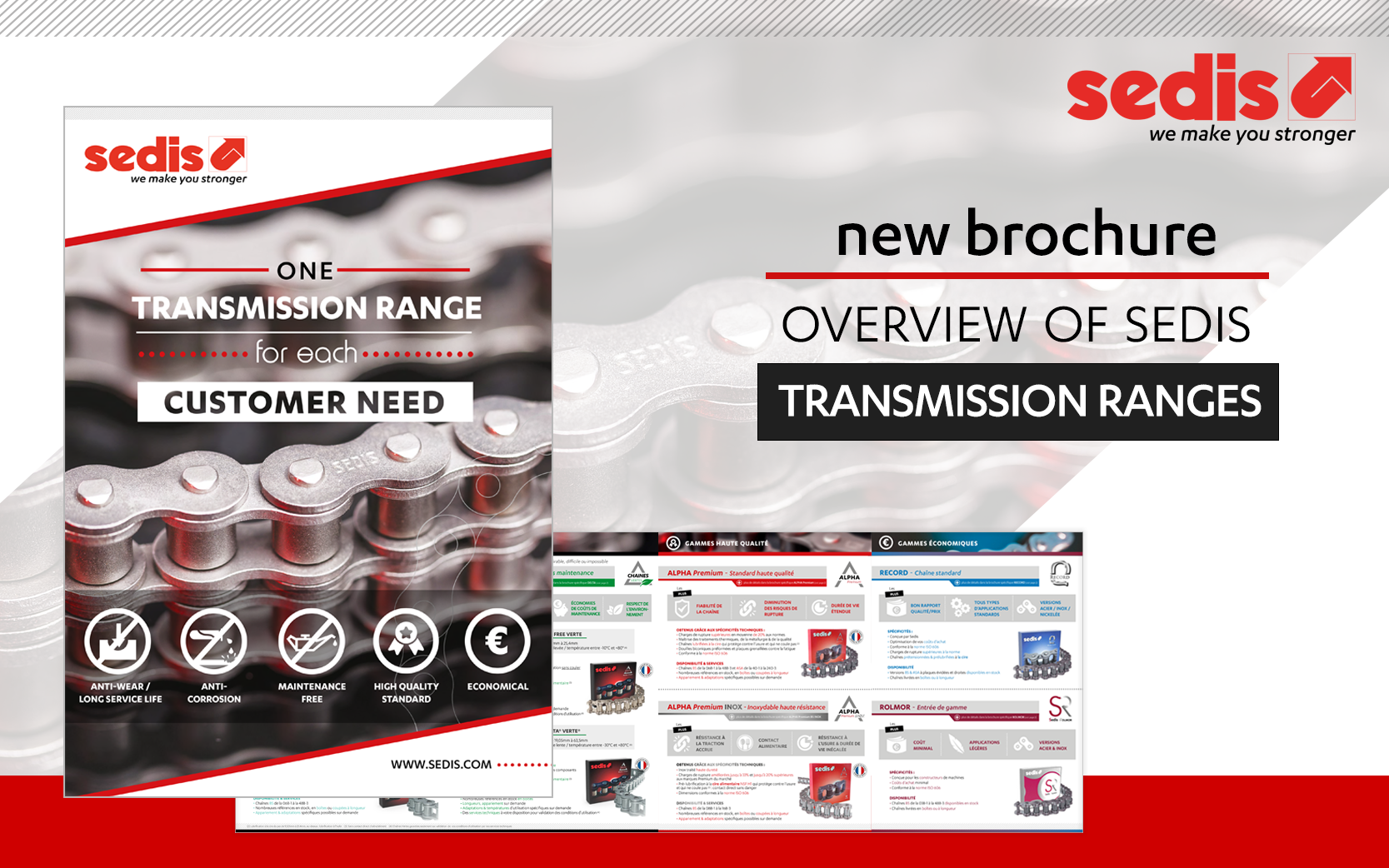
New brochure : transmission ranges overview
A global view in just one look !
See our new brochure which presents all our transmission ranges with their use, positioning, advantages and characteristics !
A global view in just one look !
See our new brochure which presents all our transmission ranges with their use, positioning, advantages and characteristics !
Trop de contraintes pour lubrifier vos chaînes ?
Découvrez notre nouvelle brochure qui présente nos gammes de solutions sans maintenance, leurs avantages et caractéristiques techniques.
Découvrez Sedis, acteur mondial concepteur de tous les types de chaines : transmission, agricole, levage, adaptée et manutention.
Notre savoir-faire allie la performance à l’excellence de pointe. Comptez sur nous pour déployer la qualité, la robustesse, l’innovation et les services que vous attendez.
Réputée et appréciée dans le monde entier, Sedis sert les enjeux de tout type d’industrie, avec une attention et une performance dédiée à nos clients.
Catalogues, brochure corporate, brochures métiers, fiches gammes… Téléchargez nos documents !
Installation / Maintenance, unités déportées de chaînes adaptées, plateforme logistique internationale, ou centre de formation, découvrez nos services !
De la technique de la chaîne aux conseils de montage en passant par les documents d’aide à la définition de la chaîne, retrouvez tous nos supports en ligne !
2 usines en France, 3 filiales en Europe et la présence de nos commerciaux dans le monde entier ! Trouvez votre contact chez SEDIS !
Découvrez le centre d’Etudes et de Recherches Sedis : nous adaptons les chaines aux nouveaux process, nous réalisons les nouveaux prototypes, les tests en laboratoire, pour mettre en place de nouveaux produits et applications novatrices.
SEDIS est fortement engagée dans une démarche de respect environnemental. A travers nos usines, mais aussi en proposant à nos clients des produits respectueux de leur environnement naturel…