Where the angle of inclination exceeds 60°, and where a vertical drive cannot be avoided, precautions must be taken to ensure proper chain-to-sprocket gearing on the power sprocket,
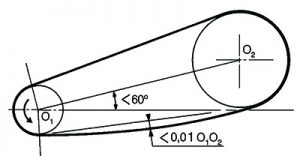
The centerline
• The tensioned strand of the chain should preferably be on the top,
• The number of sprocket teeth should be selected from the standard range whenever possible. The normal transmission ratio must not exceed 1/8. Allow for two chain drives in series for higher ratios. It is preferable if the number of sprocket teeth and the number of links are prime numbers,
• Provide shaft center adjustment to ensure that the slack section of the chain is around 1% of the drive centers, provide a further 3% adjustment to compensate for chain wear.
• Tension: initially, the chain will not require any tensioning. But, in certain applications: reciprocation drive direction, frequent stop/start operations… it is necessary to have a tensioning force on the slack strand that does not exceed 10% of the driving force on the tight strand. This can be automatically adjusted or periodically regulated manually. When either the motor torque or the driven machine loading are irregular, in addition to providing a tensioning device on the slack strand, it may be necessary to mount a guiding device on the tight strand to control vibration.
In general, it is preferable, despite introducing correcting coefficients into your calculations, to adhere to the basic principles already outlined. These include: drive shaft cen- ters, neither too short nor too long ; a drive ratio of about 3/1 ; a drive sprocket having about 25 teeth ; and ideally simplex chain, but if multiplex, with a minimum multiplicity.